What is the significance of this specific form of bleaching, and how does it contribute to the overall process?
This method of bleaching, often utilized in specific contexts, involves a particular set of techniques and chemical applications to remove unwanted color from a material, such as wood, textiles, or paper. The process carefully controls the oxidation and reduction reactions to achieve desired results. Examples might include a carefully measured bleaching process for a specific type of wood pulp, or a refined textile bleaching technique used in industry. The exact procedures and components are tailored to the specific material and desired outcome, ranging from a very mild, gentle bleaching to a more aggressive one.
The precise benefits depend on the specific application. In pulp and paper production, effective bleaching can improve the brightness and whiteness of the final product, which impacts paper quality. In textile manufacturing, bleaching can remove impurities, create uniformity in color, and facilitate the dyeing process. Historically, the evolution of bleaching methods has been a significant factor in the development of industries like paper and textiles, leading to increased efficiency and production capacity. Environmental considerations are also a vital aspect of modern bleaching processes, focusing on minimizing harmful waste products.
Moving forward, this discussion will delve into the detailed chemical mechanisms and practical aspects of this bleaching method, including the specific types of chemicals used, the process steps, and safety protocols. Additional insights into the sustainability and cost-effectiveness of this approach will also be explored.
Kubo Bleach
Understanding Kubo Bleach requires examining its essential components and processes. This detailed approach reveals the nuances and significance of this bleaching method.
- Chemical Composition
- Process Parameters
- Material Type
- Safety Protocols
- Efficiency Metrics
- Environmental Impact
The key aspects of Kubo Bleach, a bleaching method, encompass the specific chemicals used, controlled parameters during the process, suitability for various materials, stringent safety precautions, measures of output effectiveness, and the associated environmental footprint. For example, the chemical composition of a whitening agent used in Kubo Bleach will dictate its efficacy and potential hazards. Process parameters like temperature and time are critical to avoid material degradation. Selection of the suitable material type, whether paper pulp or textiles, is fundamental to achieving desired results. Safety protocols in Kubo Bleach aim to prevent accidents and minimize environmental contamination, impacting overall efficiency. Effective Kubo Bleach methods are measured by parameters like whiteness index and yield, showing how the process achieves a desired result. Finally, environmental impact must be taken into account when developing Kubo Bleach, as the chemical choice and the overall waste production affect the surroundings.
1. Chemical Composition
The chemical composition of bleaching agents is paramount to the efficacy and safety of the Kubo bleaching process. Choosing the appropriate chemicals directly impacts the bleaching outcome, material integrity, and environmental footprint. Understanding the specific chemical reactions and interactions within this process is essential.
- Oxidizing Agents
Oxidizing agents are central to Kubo bleaching. Their role is to strip color from the material by chemically oxidizing the chromophores (color-bearing molecules). The effectiveness of the oxidizing agent, its reactivity, and its compatibility with the target material directly influence the outcome. Examples include hydrogen peroxide (H2O2), sodium hypochlorite (NaClO), and various peracids, each with unique properties and applications. The choice significantly affects the bleaching speed, the degree of whiteness, and potential environmental concerns due to by-products.
- Reducing Agents (and their role in the process)
Reducing agents can play a supporting role in Kubo bleaching, in contrast to their sole oxidizing counterparts. Some materials might require reducing agents to achieve complete decolorization, or to prevent the formation of undesirable by-products. Their specific functionality is dependent on the material being bleached, and they could even participate in the process of detoxification.
- Stabilizers and Co-solvents
Stabilizers are crucial for preventing premature decomposition or unwanted reactions within the bleaching solution. They can lengthen the lifespan of the bleaching agent, improving efficiency and safety. Similarly, co-solvents might be introduced to enhance the solubility of the main bleaching agent in the reaction medium. The use of these chemicals directly affects the overall process duration and cost-effectiveness, as well as the sustainability of the bleaching method.
- pH Control Agents
Maintaining a precise pH level is critical to ensuring the optimal activity of the oxidizing agents and preventing material damage. A specific pH range is often required for efficient bleaching. Buffer solutions, acidulants, or alkalis are often used to maintain the intended pH, influencing both the bleaching effectiveness and safety precautions. Adjusting the pH level directly influences the stability and efficiency of the other components in the mixture.
The judicious selection and careful control of chemical composition in Kubo bleach are essential for achieving the desired level of whiteness and preserving the integrity of the treated material, as well as minimizing environmental impact. The optimization of the chemical components is a crucial aspect of developing cost-effective and sustainable bleaching practices.
2. Process Parameters
Process parameters are inextricably linked to the efficacy and success of the Kubo bleaching method. These parameters encompass the critical variables influencing the bleaching process, including temperature, time, concentration of chemicals, and the specific sequence of steps involved. Precise control over these factors is fundamental to achieving the desired level of whiteness, maintaining material integrity, and minimizing environmental impact. Variations in these parameters can dramatically alter the outcome, leading to either superior results or compromised material quality.
Consider the temperature of the bleaching solution. Elevated temperatures often accelerate the chemical reactions, potentially leading to a faster bleaching time. However, excessive heat can degrade the material being treated, resulting in reduced strength, discoloration, or irreversible damage. The optimal temperature range, therefore, must be carefully determined based on the specific material. Similarly, the concentration of bleaching chemicals directly affects the rate of decolorization, but excessive concentrations can lead to material damage or generate environmentally harmful by-products. Maintaining the appropriate concentration of chemicals and controlling the duration of exposure to the bleaching solution are key to achieving the desired level of whiteness without sacrificing material quality. Furthermore, the order in which different bleaching agents are introduced to the process can affect the overall outcome, creating a sequence-dependent behavior. Practical examples include adjusting the temperature and duration of bleaching in the paper industry to maintain fiber strength and optimal brightness or modifying the sequence of bleaching steps for textiles to ensure color removal without causing shrinkage. Inherent understanding of these parameters is crucial for developing and optimizing the Kubo bleaching process in various industrial settings.
In summary, controlling process parameters is essential for producing high-quality outputs while maintaining the integrity of materials in the Kubo bleaching method. Precise adjustments to temperature, time, concentration of chemicals, and solution sequences are crucial for successful execution. Deviations from the ideal parameters can compromise both the quality and the sustainability of the bleaching process. Failure to account for the intricate interplay between these parameters can result in suboptimal bleaching results and/or environmental issues, highlighting the necessity for detailed process design and rigorous control in practical applications of Kubo bleaching.
3. Material Type
The effectiveness and suitability of the Kubo bleaching process are significantly influenced by the type of material being treated. The inherent properties of the materialits chemical composition, structure, and inherent colordictate the optimal approach for bleaching. This aspect is crucial for achieving desired outcomes while minimizing potential damage or degradation.
- Chemical Composition
Different materials possess varying chemical structures that affect their response to bleaching agents. Certain materials might contain complex organic molecules that resist decolorization, requiring tailored bleaching strategies and potentially multiple steps. Conversely, materials with simpler structures might be more readily bleached. For example, cellulose-based materials like wood pulp react differently to bleaching agents compared to protein-based materials like cotton or wool. This inherent difference in chemical composition dictates the specific chemical agents and conditions needed for efficient and safe bleaching.
- Structure and Fiber Morphology
The physical structure of the material greatly impacts the penetration of bleaching agents and the uniformity of the bleaching process. Dense materials may require more aggressive treatment to achieve complete decolorization. The presence of fibers, such as in textiles or paper pulp, significantly influences the effectiveness and uniformity of the bleaching process, with certain fiber morphologies exhibiting more or less resistance to bleaching agents. The size and arrangement of the fibers affect the penetration depth and the extent to which individual fibers are affected by the bleaching solution. Proper consideration of fiber structure is critical for achieving uniform decolorization and maintaining the structural integrity of the material.
- Initial Coloration
Pre-existing coloration in the material can influence the bleaching process. The type and intensity of the initial color significantly impact the bleaching agent needed to achieve the desired final shade. Materials naturally colored, such as wood with dark pigments, require a different approach compared to uncolored or naturally light materials. The nature of the coloring substances or pigments within the material directly dictates the choice and effectiveness of the bleaching agents and process parameters.
- Mechanical Properties
The mechanical properties, such as tensile strength and durability, of the material must be considered during bleaching. Some bleaching agents can weaken fibers or create undesirable effects on the overall mechanical integrity of the material. For example, extremely aggressive bleaching procedures may cause significant structural damage in certain textiles. The desired outcome, alongside any limitations on the materials ability to withstand the bleaching process, guides the choice of bleaching conditions.
Ultimately, careful consideration of the material type in the Kubo bleaching process is crucial. Matching the appropriate chemical agents, conditions, and steps to the specific characteristics of the material is essential for achieving the desired level of decolorization and maintaining material integrity, minimizing environmental impact, and achieving cost-effectiveness.
4. Safety Protocols
Effective implementation of safety protocols is paramount in the Kubo bleaching process. These protocols are crucial for worker safety, environmental protection, and the successful execution of the bleaching process itself. Adherence to established safety measures directly impacts the prevention of accidents, minimizes environmental contamination, and ensures the maintenance of material integrity throughout the process. Neglecting these protocols can lead to serious consequences.
- Chemical Handling and Storage
Proper handling and storage of bleaching agents are essential. Bleaching chemicals often possess hazardous properties, such as corrosivity, flammability, or toxicity. Appropriate personal protective equipment (PPE) must be utilized during all stages of chemical handling. This includes gloves, eye protection, and respirators, tailored to the specific chemicals involved. Storage facilities must comply with regulations, ensuring secure containment, proper ventilation, and clear labeling to prevent accidental exposure or misuse. Spill response procedures must be readily available and practiced, guaranteeing swift and effective action in case of a chemical spill.
- Ventilation and Air Quality Monitoring
Adequate ventilation in the bleaching area is critical to remove potentially harmful fumes and vapors produced during the process. Effective ventilation systems must be in place to prevent the buildup of hazardous gases or dust particles, maintaining acceptable air quality. Continuous air quality monitoring and regular maintenance of ventilation systems are essential to safeguard worker health and maintain a safe environment. The type and degree of ventilation needed will depend on the specific bleaching chemicals used.
- Equipment Maintenance and Inspection
Regular maintenance and inspection of equipment involved in the Kubo bleaching process are crucial. Equipment malfunctions, especially with pressure vessels, pumps, or mixing units, can lead to catastrophic consequences. Regular inspections by qualified personnel are needed to identify and rectify potential hazards. This proactive approach ensures the equipment remains in optimal condition, minimizing the risk of leaks, spills, or explosions. Appropriate safety interlocks and alarms should be present to provide early warning in case of anomalies.
- Waste Disposal and Environmental Regulations
Proper disposal of chemical waste generated by the Kubo bleaching process is essential to protect the environment. Wastewater and solid waste must adhere to environmental regulations and appropriate disposal procedures. Adherence to relevant legislation ensures that toxic or hazardous waste is not released into the surrounding environment. Waste materials must be segregated according to their properties, and appropriate containers used for transportation and disposal to prevent contamination or environmental damage.
Strict adherence to safety protocols throughout all phases of the Kubo bleaching process is critical. These protocols not only safeguard the well-being of workers but also protect the environment and ensure the long-term sustainability of the process. By prioritizing safety, risks can be minimized, allowing for a more reliable and efficient implementation of the bleaching method. This approach is essential for maintaining a responsible and sustainable industrial practice.
5. Efficiency Metrics
Quantifying the efficiency of the Kubo bleaching process is crucial. Precise measurement of key performance indicators (KPIs) allows for optimization, cost reduction, and environmental sustainability. Metrics provide data-driven insights into the effectiveness of the bleaching process at different stages. This data enables comparison of various methods and ultimately contributes to refining the overall procedure.
- Bleaching Rate
Bleaching rate, measured as the speed at which color removal occurs, is a fundamental efficiency metric. A rapid and consistent bleaching rate suggests an optimized process. This can be quantified by monitoring the rate of color removal over time, usually with spectrophotometric measurements. Higher bleaching rates often translate to reduced processing time, lowered operational costs, and greater throughput.
- Yield and Loss Rates
Yield, the amount of usable product obtained relative to the input, and loss rate, the proportion of material lost during the process, are crucial indicators. High yield and low loss rates are desirable for cost-effectiveness. Optimizing chemical usage, refining the bleaching sequence, and minimizing byproduct formation can directly impact yield and minimize material loss. Precise measurement and analysis of yield and loss throughout the process are necessary for identifying and addressing bottlenecks.
- Energy Consumption
Energy consumption is a significant factor in the overall cost of the bleaching process. Minimizing energy input, especially through adjustments to operating temperature and pressure, directly contributes to efficiency. Monitoring and analyzing energy consumption helps identify potential areas for optimization and the implementation of more sustainable bleaching methods, such as utilizing renewable energy sources whenever possible.
- Chemical Usage and Cost
Precise monitoring of chemical usagespecifically, the amount of bleaching agents requiredand the corresponding costs provides crucial information. Minimizing chemical use while maintaining effectiveness is a key efficiency goal. This can be achieved through process optimization and the use of more concentrated solutions, lowering the cost per unit of material bleached and contributing to cost efficiency.
By analyzing these efficiency metrics in the Kubo bleaching process, industries can identify opportunities for improvement. Optimizing the bleaching rate, yield, energy consumption, and chemical usage allows for enhanced cost-effectiveness, reduced environmental impact, and improved sustainability. Regular monitoring and analysis of these metrics are paramount to continuous improvement in the Kubo bleaching procedure and the overall competitiveness of the industrial sector.
6. Environmental Impact
The environmental impact of the Kubo bleaching process is a critical consideration. This encompasses the effects of the bleaching agents, the energy consumed, and the waste generated on the surrounding ecosystem. The choice of chemicals, the intensity of the process, and the subsequent waste disposal procedures all contribute to the environmental footprint. A thorough understanding of these factors is essential for responsible industrial practices. For instance, certain bleaching agents, if not properly managed, can release harmful pollutants into water sources or the atmosphere. The energy consumption associated with the bleaching process contributes to overall carbon emissions, potentially exacerbating climate change.
Minimizing this impact requires careful selection of bleaching agents with reduced toxicity and environmental persistence. The use of renewable energy sources to power the bleaching process, as well as the implementation of closed-loop systems for waste management, are crucial. Furthermore, advanced treatment methods for wastewater discharge can significantly decrease the environmental impact of bleaching effluents. Practical examples of successful implementation of these measures exist in certain industrial settings, demonstrating their positive impact. For instance, companies transitioning to ozone-based bleaching solutions, known for their lower environmental impact, or those employing sophisticated wastewater treatment technologies to neutralize harmful by-products, are actively reducing their ecological footprint. Moreover, the optimization of bleaching processes, allowing for the use of smaller quantities of chemicals and less energy, plays a significant role in achieving a more environmentally responsible approach.
In conclusion, the environmental impact of Kubo bleaching is an intricate and multifaceted issue. Careful consideration of chemical choices, energy usage, and waste disposal is essential for minimizing the negative environmental consequences. Adopting environmentally responsible practices is not just a matter of compliance but also a crucial element for ensuring long-term sustainability and profitability. Industries committed to reducing their ecological footprint through process improvements and technological innovations are likely to achieve a more sustainable and environmentally sound Kubo bleaching process, laying a foundation for wider industry adoption of environmentally responsible practices. Addressing this issue directly improves the overall image and reputation of the sector.
Frequently Asked Questions about Kubo Bleach
This section addresses common inquiries regarding the Kubo bleaching process. The following questions and answers provide clarity on key aspects of this method.
Question 1: What are the key chemical components typically employed in the Kubo bleaching process?
The specific chemical makeup of Kubo bleaching solutions varies depending on the material being treated. However, oxidizing agents are central, often including hydrogen peroxide, sodium hypochlorite, or various peracids. Reducing agents may also be present in certain processes to facilitate complete color removal or to mitigate unwanted by-products. The precise blend is optimized for a given material and application.
Question 2: How does the Kubo bleaching process impact the structural integrity of the treated material?
The effect on material structure depends on the material type and the specifics of the Kubo bleaching process. Certain agents and procedures can potentially weaken fibers or cause damage, particularly if parameters such as temperature, concentration, or time are not carefully controlled. Adequate safety protocols are essential to minimize structural degradation.
Question 3: What are the primary safety considerations associated with Kubo bleaching?
Safety is paramount. Proper handling and storage of chemicals are crucial, requiring appropriate personal protective equipment (PPE). Adequate ventilation is essential to mitigate exposure to harmful fumes or vapors. Disposal of chemical waste must strictly adhere to environmental regulations to prevent pollution. Thorough training and adherence to established safety protocols are critical.
Question 4: How does the Kubo bleaching process compare to other bleaching methods, like chlorine-based methods?
Kubo bleaching methods may offer advantages in terms of environmental impact. Different bleaching procedures have varying environmental footprints, and Kubo bleaching aims to minimize the release of harmful by-products. Specific methods for wastewater treatment are usually an integral part of a Kubo bleaching approach. A thorough comparison requires detailed evaluation of specific procedures.
Question 5: What factors determine the energy consumption in the Kubo bleaching process?
Energy consumption in Kubo bleaching is influenced by several factors, including the size of the batch, the required temperature for the reaction, and the specific chemical solutions used. Process optimization and the implementation of energy-efficient technologies are key to minimizing energy expenditure. Using renewable energy sources can contribute to further sustainability.
Understanding the detailed process considerations surrounding Kubo bleaching, including the specific chemicals used, the controlled parameters, the chosen material, and the related safety procedures, is fundamental for practical application. The proper execution of this method ensures both optimal results and minimized environmental impact.
The following sections provide further details on the Kubo bleaching process, examining the specific chemical mechanisms, practical considerations, and optimization strategies.
Conclusion
The Kubo bleaching process, a crucial technique in various industries, necessitates meticulous control over numerous parameters. Chemical composition, process parameters, material type, safety protocols, efficiency metrics, and environmental considerations all play critical roles in its successful and sustainable application. Optimal bleaching outcomes hinge on the precise selection and careful management of oxidizing and reducing agents, along with the precise control of temperature, time, and concentration. The choice of material significantly affects the bleaching process, requiring tailored approaches to preserve material integrity. Strict adherence to safety protocols is paramount to mitigate risks to workers and the environment. Efficient implementation of Kubo bleach is reflected in high bleaching rates, optimized chemical usage, minimized waste, and reduced energy consumption. Environmental impact is minimized through judicious chemical selection, waste management strategies, and energy efficiency measures. These multifaceted aspects underscore the complexity and significance of Kubo bleaching in industrial applications.
Moving forward, continued research and development are vital to enhance Kubo bleaching's efficiency and reduce its environmental footprint. Optimizing existing processes and exploring innovative alternatives will improve the long-term viability of this method. Addressing environmental concerns through the development of sustainable bleaching agents, closed-loop systems, and alternative energy sources is crucial for responsible industrial practices. The meticulous understanding and precise implementation of Kubo bleaching remain essential for maintaining high standards of product quality and environmental stewardship within relevant industries. The continued evolution of this technique will be integral to the future success and sustainability of numerous sectors.
Ronnie Spector Death: Cause & Details Of Singer's Passing
Wes Welker: Date Joined & Career Highlights
Steve Allen Tonight: A Night Of Laughter & Legends

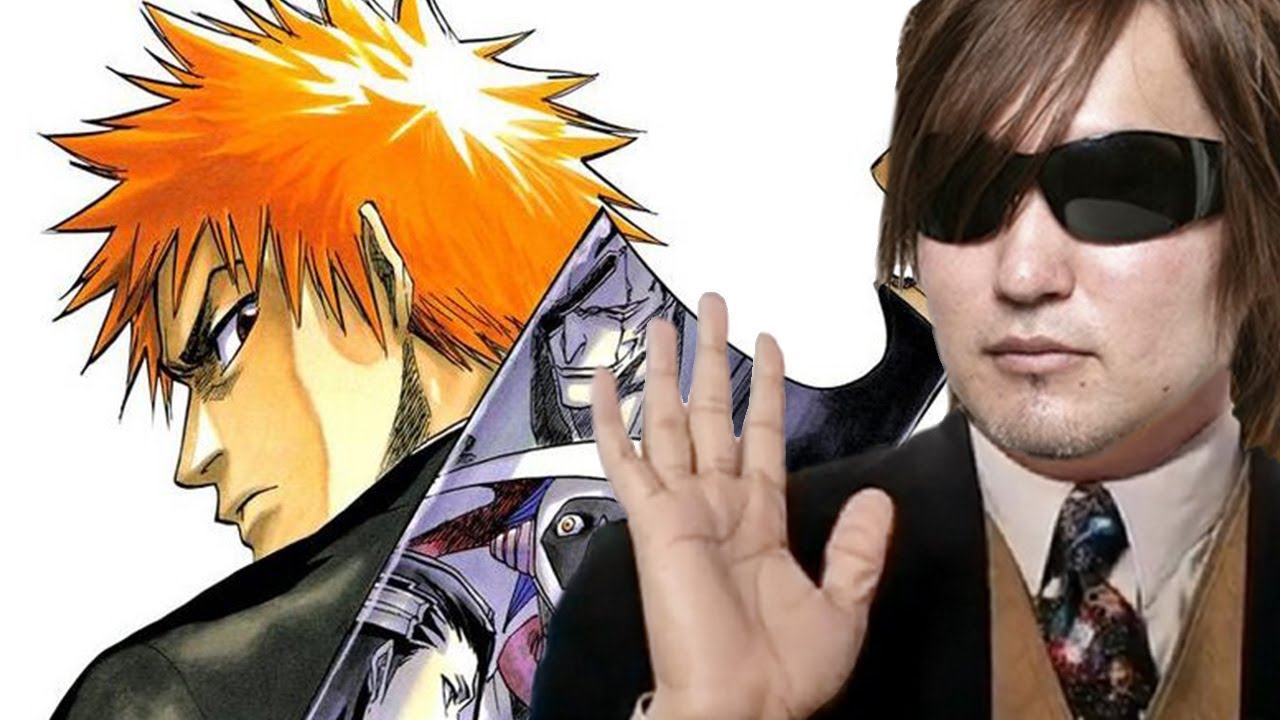
![[Art] Kubo had one sick sense of fashion (Bleach) r/manga](https://i2.wp.com/preview.redd.it/yn6qfwsbyqa31.jpg?auto=webp&s=be622a5797b2a26d1c486360b9641b36f646392a)